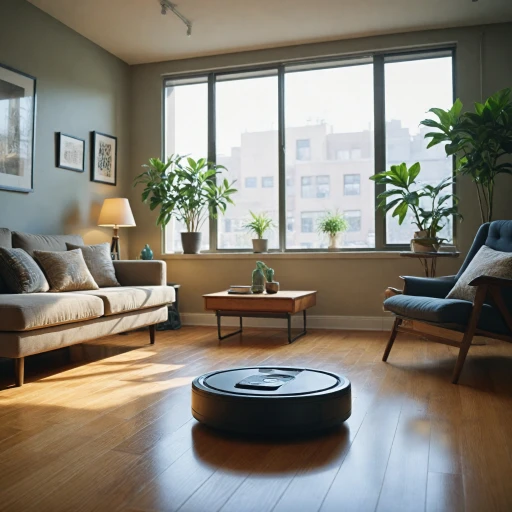
What is an End Effector?
Exploring the Core Components of a Robot Vacuum
Understanding the role of an end effector is crucial in grasping how robot vacuums function efficiently. An end effector is essentially the component at the end of a robotic arm or system that interacts with the environment to perform specific tasks. In the context of robot vacuums, these effectors are responsible for carrying out actual cleaning tasks such as picking up dust and debris. Robot vacuums come equipped with various types of end effectors specifically designed for different applications. These include brush systems, suction cups, and vacuum generators, each serving a unique purpose. For instance, brush systems are tailored to sweep and gather dirt, while vacuum generators use suction to ensure thorough cleaning. The development of these robotic effectors involves integrating force compliance features, allowing them to adapt to different surfaces effectively. Torque sensors play a crucial role in measuring the resistance encountered by the robot, ensuring optimal force is applied during cleaning. This enables the robot effector to handle a wide range of surfaces, from metal to plastic, with precision. In essence, these end effectors are comparable to human fingers in a way that they perform tasks like gripping, picking, and placing items, albeit at a much smaller scale. With advanced technologies, robot vacuums are becoming increasingly adept at navigating complex environments and executing tasks with the accuracy of industrial robotic arms. To gain a deeper understanding of these innovative technologies, you can check out the article on exploring the fascinating world of robot vacuums. This resource offers an insight into the capabilities of robot vacuums, driven by sophisticated end effectors.Types of End Effectors in Robot Vacuums
Diverse Gripping Tools in Robot Vacuums
The world of robot vacuums showcases a fascinating array of gripping tools designed to tackle a wide range of cleaning tasks. These tools, known as end effectors, are integral to the vacuum's performance and adaptability. Each type of effector is tailored to perform specific functions that help the robot navigate, clean, and interact with different surfaces and objects.
Suction cups are one of the most common effectors used in robot vacuums. They use vacuum generators to create a suction force that allows the robot to grip and maneuver on various surfaces, whether it's carpet or hardwood. Suction cups require precise torque sensors to avoid excessive force, ensuring gentle handling while maintaining strong contact with the surface.
In addition to suction systems, some robot vacuums are equipped with finger grippers, which act similarly to robotic arms. These grippers are proficient at pick and place applications, moving debris from one point to another. The grippers may incorporate advanced sensors to adapt to different textures and shapes, enhancing the vacuum's ability to handle diverse cleaning scenarios efficiently.
Metal and plastic components are often used in manufacturing these effectors, as they provide the necessary strength and flexibility for enduring repeated use. Robotic effectors such as the robotic arm and effector robot showcase how technology merges with practicality, resulting in highly effective cleaning solutions. As robotic arm technology advances, these systems include force compliance capabilities to adjust the applied force, ensuring precise and safe operations.
Understanding the types of end effectors employed in robot vacuums is essential to appreciating their capabilities and limitations. These innovations continue to evolve, aiming to fine-tune the user experience by making these robotic systems more adaptable and efficient.
Technological Advancements in End Effectors
Technological Leap in Robotic Effectors
The world of robot vacuums has seen significant advancements, particularly in the development of end effectors. These important components play a pivotal role in enhancing the capabilities of robotic arms used in various applications. As technology progresses, robotic effectors continue to evolve, improving efficiency in tasks like handling and surface finishing.
Key innovations in end effector technology include the integration of sensors and precision tools, which allow effector robots to tackle complex tasks with greater dexterity. Vacuum generators and suction cups are among the different types of effectors that have become more effective due to recent technological improvements. Robotic arms are now equipped with advanced gripping mechanisms such as finger grippers and vacuum grippers, enhancing their pick and place abilities.
With the integration of torque sensors and force compliance systems, robotic arms can handle delicate items like those made from metal or plastic more precisely. This precision is crucial for tasks that require gentle handling, such as machine tending. Additionally, adaptive force control allows robotic systems to adjust their gripping force in real-time, which is a significant step forward in effector technology.
These technological advancements are widening the scope of applications in which robots can be employed, offering more competent and efficient solutions suited to a wide range of environments—from everyday household tasks to the more specialized demands of industrial settings. Together, these innovations in effector technology continue to improve the user experience, making robots more reliable and adept at meeting the needs of modern society.
Challenges in Designing End Effectors
Design Challenges and Engineering Nuances
Designing end effectors for robot vacuums is no easy feat, presenting a matrix of challenges and complexities for engineers. These effectors, crucial for the machine's functionality, have to be meticulously crafted to cater to the unique tasks that a robot vacuum must perform.
One significant challenge lies in the integration of sensors and systems that aid in the precise execution of cleaning tasks. The robot's end effector must be compatible with a range of sensor technologies, such as torque sensors and force compliance systems, that help maintain optimal contact with different surfaces, be it metal or plastic. These sensors play a crucial role in providing feedback that guides the robotic arm in achieving efficient handling and surface finishing.
Another engineering hurdle is the selection and optimization of gripping tools like suction cups and finger grippers. These are vital for the pick and place capabilities of robot vacuums, allowing them to effectively adapt to various applications and surface types. Different types of effectors, such as vacuum generators, need to be equipped to handle a wide range of particles, debris, and dust, ensuring thorough cleaning without manual intervention.
Additionally, the structural aspect of the robot arm and effector robot demands careful consideration. Designers must account for the robot's force and gripping capabilities to avoid any potential damage to the vacuums or surroundings while maintaining high efficiency and productivity in tasks.
Balancing these requirements calls for seamless integration and coordination of robotic systems, which can prove daunting for any design team. Yet, overcoming these obstacles is essential to enhancing the robot vacuum's performance and end-user satisfaction.
Impact of End Effectors on User Experience
Enhancing the User Experience with Advanced End Effectors
The user experience is significantly impacted by the sophisticated design of end effectors in robot vacuums. These robotic components are crucial as they handle various tasks autonomously, ensuring efficient cleaning processes.The introduction of different types of effectors, such as finger grippers and vacuum grippers, has played a vital role. These components allow robot vacuums to adapt to different surfaces, ensuring effective cleaning across a wide range of environments. Suction cups and vacuum generators assist in the precise pick and place tasks, enabling thorough interaction with different floor types including metal and plastic surfaces.
Sensors integrated into the robotic systems are essential for detecting obstacles and adjusting the vacuum's movements. Technologies like force compliance and torque sensors ensure that the robotic arm or arm effector adapts to varying forces, enhancing the cleaning efficiency while minimizing possible damage to delicate surfaces.
Effectors facilitate handling and figure prominently in the automation of tasks, securing a seamless user experience. This translates to less manual intervention, as robotic arms and tools perform with precision and consistency. Users find confidence in the robot's ability to navigate and clean autonomously, a crucial factor in the growing adoption of these machines in everyday applications.
Through continuous advancements in robotic effectors, future systems promise to deliver even more intuitive and adaptive cleaning solutions, further enhancing the user experience.